Gamuda IBS way to build homes for the future
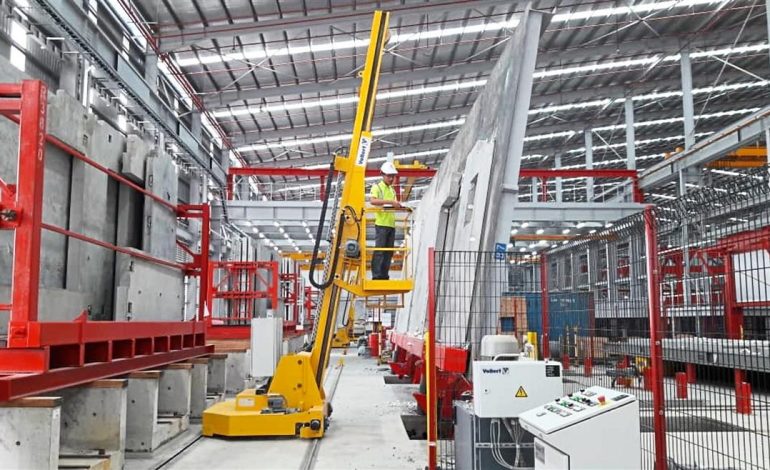
Players in the Malaysian construction sector are largely familiar with the industrialised building system (IBS), which has undergone tremendous evolution since it was first trialled here in the 1960s.
By now, IBS is already recognised worldwide, especially in developed countries, as having the advantage of providing quality finished products – which is important for the precast concrete system used for housing. These include components such as walls, slabs, columns and other three-dimensional units such as bathroom/toilet pods.
For Gamuda Bhd, moving into a sophisticated IBS production line was important to raise overall quality of buildings by optimising the use of resources such as cement, sand and steel as well as contributing to lessening the country’s reliance on foreign labour in the construction sector.
It made its first foray into the construction industry on a large scale in 2016 when it unveiled its brand-new IBS factory in Sepang, Selangor, to the world. The plant that sits on a 11ha-site makes solid walls, half slabs, staircases, toilet pans, columns, beams, as well as special architectural elements.
These components have been installed for the Rumah Selangorku (RSKU) 714 apartments at Gamuda Land’s Jade Hills project in Kajang where happy buyers of the Gapura Bayu units will be receiving their keys anytime this month, almost a year ahead of schedule.
Gamuda Industrial Building System Sdn Bhd (Gamuda IBS) general manager Tan Ek Khai credits Gamuda’s use of a sophisticated digital IBS set-up as a major contributing factor to the ability of the developer to meet, in this case surpass, the timeline.
Gamuda IBS places a premium on a fully computerised system that employs extensive use of automation and robotics to produce the high-quality products which meet extremely tight tolerances. All this happens under a controlled climate factory that reflects its philosophy summed up in one word: Gamuda IBS.
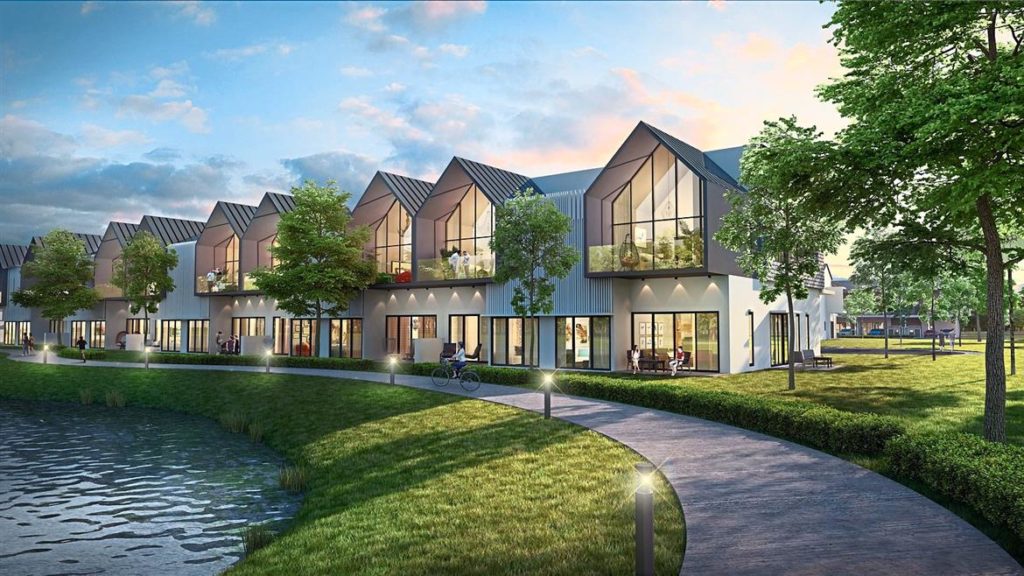
Digital IBS
“Gamuda IBS provides flexibility in design, while ensuring fast construction and superior quality finish,” said Tan.
“Speed-wise, we are unmatched in that we are able to produce and install IBS panels at a rate of one floor each week for high-rise apartment units measuring 900sqft (84sqm). Looking at it another way, we are able to manufacture components for such apartment units at one unit every hour. With this kind of speed, traditional floor-by-floor casting cannot compete with us,” he said.
Gamuda is putting its money where its mouth is, as it is now ready to unveil its second IBS factory at a 27ha-site in Banting, Selangor. And with this, it is now further marketing its prowess as “digital IBS’’, where an even greater level of data processing and automation are introduced to further streamline the manufacturing process, drawing upon the lessons learned from operating the Sepang factory in the last two years.
The Banting factory makes solid walls, double walls, pre-stressed half slabs, bathroom pods and special façade elements. This latest addition to the family is critical as it has made Gamuda IBS a fully digital end-to-end IBS solutions provider.
And this is where regulatory authorities in charge of public housing should take note. Well-built housing units using IBS can now go beyond 25 floors.
The Banting factory’s ability to make double walls, which are much stronger than single walls made by the Sepang factory, now enables developers to build all the way up to 50 floors – giving authorities more leeway to optimise scarce resource like limited land.
Capacity-wise, the Banting factory can make about 7,000 units of housing each year, more than double that of the Sepang factory (3,000 units a year), giving Gamuda IBS a total output capacity of 10,000 units of housing each year.
“Leveraging on today’s digital design tools and robotic construction, digital IBS means flexibility in design, fast construction and superior quality finish,” said Tan, who added that Gamuda is ready to meet the Government’s aim to build 200,000 units of affordable housing from now until 2020. This is on top of Gamuda IBS building all of Gamuda Land properties.
The use of Building Information Modelling (BIM) in the design process for housing complexes built with Gamuda IBS means there is no chance for design clashes, a situation where piping and plumbing may intrude into each other’s space, or where the layout of ducting or other structural members may not be optimal for construction or the needs of the end user.
At Gamuda IBS, the BIM design data is on a digital platform that is accessible to all relevant parties such as architects, structural engineers and electrical engineers. By having all design data on a collaborative platform, design clashes are resolved before construction begins or materials are procured.
The system even takes on part of a quantity surveyor’s work as it can calculate with high precision the amount of cement, sand, aggregates and steel reinforcement needed.
“The fast construction method we employ means construction duration will be reduced by 12 months – from the usual 36 to 24 months. Depending on location and design, we may be able to cut it down even further, especially with our bathroom pods in play,” said Tan.
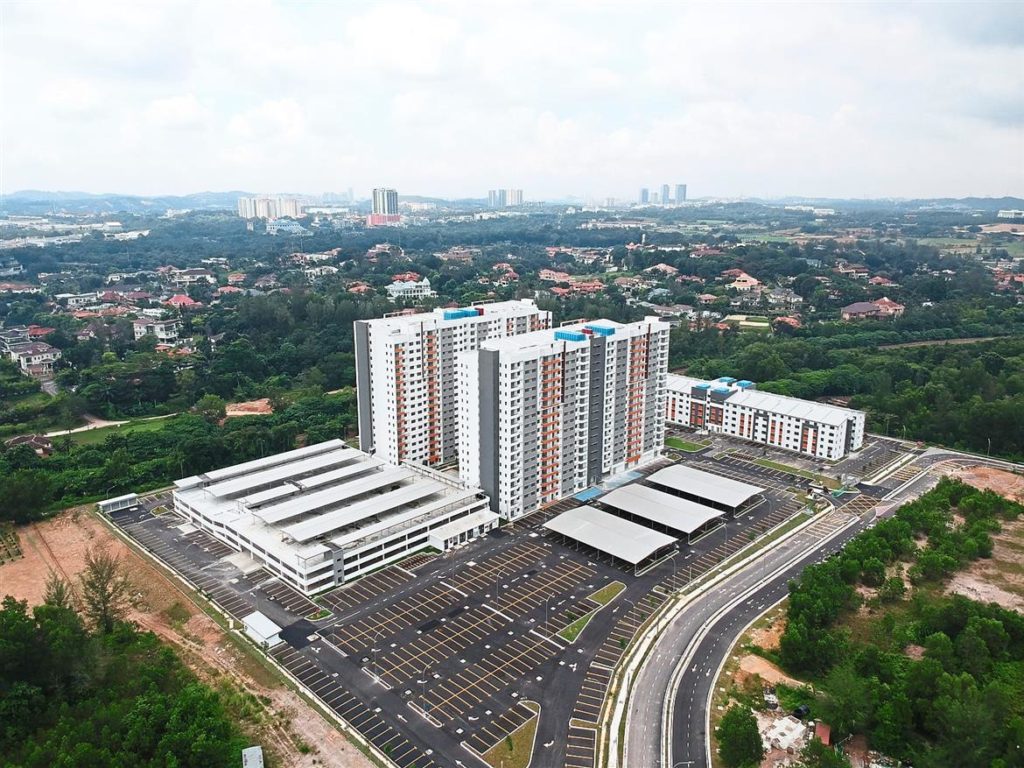
What about quality?
Gamuda IBS is committed to quality finish by aiming to score high in the Quality Assessment System for Building Construction Works (or Qlassic), administered by the country’s Construction Industry Development Board (CIDB).
Qlassic was developed in response to long-standing complaints that construction quality is a highly subjective matter, given that it is sometimes difficult to define and to quantify.
However in 2005, CIDB worked with public and private stakeholders to develop the construction industry standard, which forms the basis for some basic quality requirements that developers must meet, though project certification by Qlassic still remains voluntary now.
“Average Qlassic score for housing projects here that elect to have their projects independently-assessed hovers around 75 to 76 points (out of 100).
“As for Gamuda, we aim to meet at least 80 points for each project we develop, and will definitely not be satisfied with a mere mid-to-high 70s score,” said Tan who also revealed that as of October 2018, Gamuda has completed 1,800 units using digital IBS.
Meeting such tight tolerances calls for a well-trained workforce capable of operating computers and maintaining the army of robots and machinery that do the cutting, welding, concrete batching, concrete pouring and other functions.
Concrete casting is done indoors with the product receiving curing or hardening under climate-controlled curing chambers so that the proper strength and smooth finish can be consistently achieved.
Naturally, CIDB is supportive of more IBS usage and in its Construction Industry Transformation Plan, it proposed the improvement of quality standards by increasing implementation of quality assessments such as the Qlassic.
“This system assesses contractor workmanship and broader quality assurance for construction of buildings, which will lead to improvements in quality of both contractors and overall construction work,” it said on its website.
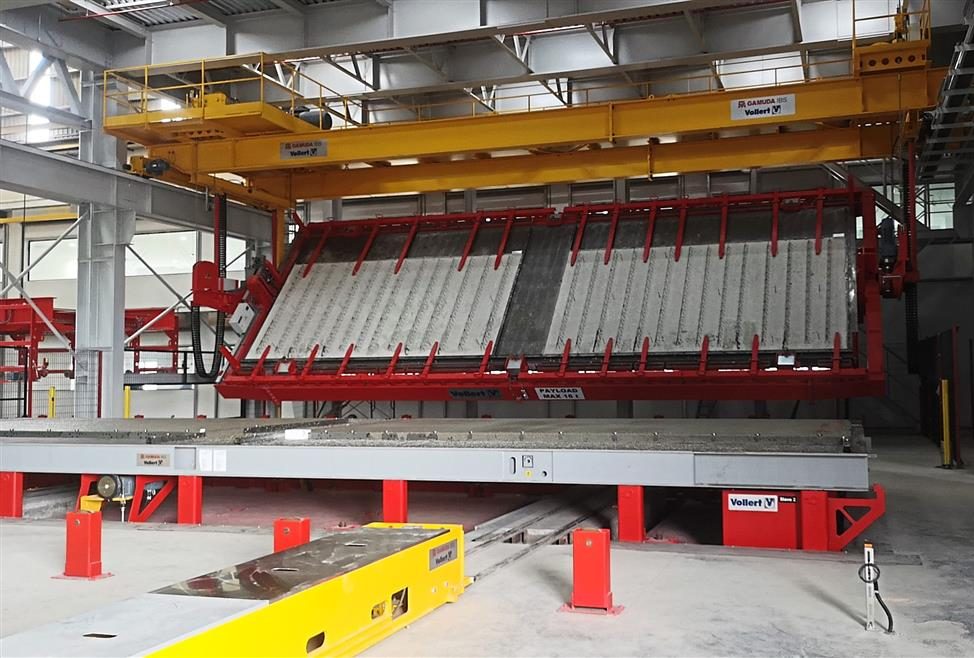
Meeting future needs
The widespread adoption of IBS also falls into the overall aim to transform the delivery process of housing to Malaysians. According to the Real Estate and Housing Developers Association Malaysia (Rehda), the time is ripe for the industry to change the way housing is delivered.
Speaking to Rehda Institute recently, Rehda chairman Datuk Jeffrey Ng acknowledged that affordable housing has a huge market.
“We have always advocated that affordable housing requires the right affordable housing ‘living ecosystem’ and that the public sector should undertake social housing whilst the private sector undertakes market-driven products which can include market-driven affordable housing,” Ng said.
“The Housing Minister’s recent announcement that various government agencies dealing with affordable housing provision are to be consolidated, coordinated and streamlined under the Housing and Local Government Ministry is a good first step towards this direction,” he added.
Tan said there had always been a gap in delivering quality affordable homes because the design was manually built using human labour.
“The Government is committed to changing the way we build, towards a more efficient, productive, cleaner and greener construction ecosystem that is less reliant on manual, foreign labour.
“We have taken a bold step in pursuing an alternative way of building that will raise productivity and upskill the local workforce with the latest technological tools, in line with the Fourth Industrial Revolution,” Tan added.
Within the group, its current order book includes RSKU Kundang Estates, RSKU Gamuda Gardens, RSKU Cybervalley, Worldwide Puncak Bestari, Gaia Residences at Gamuda Gardens, Amber Residences at Twentyfive.7 and link houses at Gamuda Cove.
As further testament to its quality control process, Gamuda IBS is also producing components for at least seven other public-listed developers, proving that many developers are seeing the upside of factory-built developments.
“With the widespread adoption of IBS, the Government can expect to deliver more homes with less investments compared to conventional practices, as construction using Gamuda IBS requires less working capital, less delivery cost, and a shortened timeline,” Tan concludes.